The 3DMorphic Difference
Every patient and surgery is unique, therefore customisation is key.
3DMorphic Patient Specific Implants are designed to have a snug fit. This provides an even load distribution and increased contact surface area between the implant and patient anatomy, promoting early onsite bone growth and stable fixation, which can result in a higher patient quality of life. Our implants require reduced intra-operative endplate remodelling, resulting in an even distribution of low strain across the endplate bone, more consistent patient results, and simpler procedures for surgeons. 3DMorphic customise implants for the desired alignment, correction, screw trajectory and surgical technique, making us the ideal patient specific solution for spinal fusion.
Better Fitting Implants
Our patient specific implants are engineered to fit with the patient's unique anatomy, ensuring immediate stability and promoting faster fusion. This snug fit ensures even load distribution and proximity between the implant and bone, setting the right conditions for bone fusion.
Controlled alignment
Achieving correct anatomical alignment aids with pain relief and prevents adjacent segment disease, avoiding further complications.
Fast to Manufacture
3DMorphic's vertically integrated manufacturing facility enables the just-in-time production of quality Patient Specific Implants for complex and general cases.
Simple Procedures
3DMorphic supports healthcare professionals by integrating pre-planned angles, corrections, and surgical approaches directly into implant designs. Helping to reduce intra-operative time, risk, and stress.
Better Load Sharing
3DMorphic implants require minimal surgical remodelling of vertebral endplate bone compared to generic implants. This technique maintains the strong endplate bone and results in even load distribution between implant and bone.

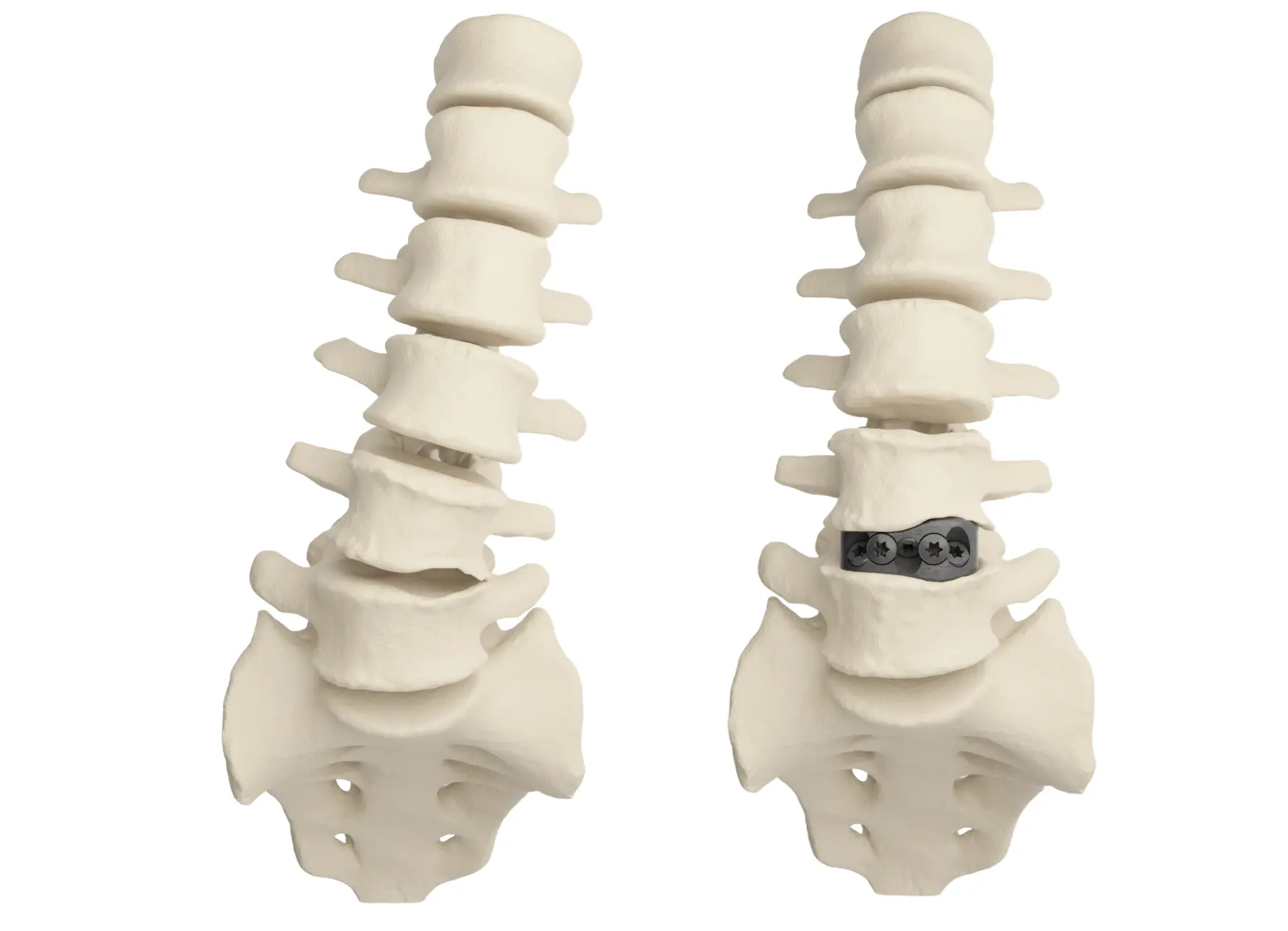



End-To-End Support
Our commitment extends beyond just the implant. We provide a seamless experience by providing biomodels, virtual surgery planning, instrumentation and intra-operative support with each 3DMorphic implant.

Biomodels
3D-printed anatomical models can be supplied with each implant, enabling surgeons to perform procedures using accurate patient specific replicas.

Virtual Surgery Plan
A Virtual Surgery Plan (VSP) is provided for each case and can include procedural aims, workflow, approach, vascular considerations, cage correction, screw trajectory and more. The VSP can be used as a pre-operative planning tool to visualise the procedure and reduce intra-operative risk.

Instrumentation
Surgical instrument sets tailored to the needs of each procedure are provided to ensure smooth implantation of 3DMorphic devices.
Custom instruments meeting specific surgeon requirements can also be provided.

Intra-Operative Support
Our expert team provides guidance and support throughout the surgical procedure.
.webp)
Post-Operative Analysis
An in-depth study can be provided analysing clinical, radiographic and 3D alignment outcomes.
FAQs
The 3DMorphic Patient Specific Implant is a spinal fusion cage designed to fit the anatomy of each patient. Spinal fusion cages are implantable devices fixed between two vertebral bodies of the spine, fusing the bone together, decompressing nerves, providing stabilisation and pain reduction.
3DMorphic Patient Specific Implants are indicated for patients with the following conditions: Degenerative Disc Disease (DDD), disc bulging or herniation, spinal stenosis resulting in myelopathy, foraminal stenosis resulting in radiculopathy, and pseudoarthrosis of two or more adjacent spinal interbody levels. We can provide custom implants for cervical, thoracic and lumbar spine regions for routine to complex cases.
All aspects of the 3DMorphic cage design and manufacture are optimised through cutting edge science and clinical evidence. See published articles for more information.
All implantable devices must be ordered by a qualified spinal surgeon.
Contact our knowledgeable Medical Representatives, who will guide you through the ordering process. All we need is the patient’s CT scan, operative requirements and the level indicated for surgery.
As soon as the patient is indicated for surgery and has a CT scan.
In saying this, 3DMorphic is a vertically integrated, Australian manufacturer, which enables us to produce Patient Specific Implants with a rapid turn-around time of under 48 hours for emergency cases.
3DMorphic designs three implant size options for each level indicated for surgery. All implants are designed to fit by maintaining the optimal contact footprint but differ in height and lordotic angle.
Different implants sizes provide intra-operative options to accommodate for the variance in the amount of soft tissue release and distraction achieved during the surgery, which can be difficult to predict prior to surgery.
3DMorphic conducted a study that demonstrates the biomechanical consequences of surgical remodelling to fit OTS implants in the interbody space.
The study found that leaving the endplate bone shape intact and using Patient Specific Implants results in more even strain distribution, preserving the bone's strength and potentially reducing post-operative complications such as implant subsidence. The patient specific approach eliminates the need for extensive surgical reshaping, reducing operating time, complexity and uneven strain in the bone.
Some might think that a risk of using Patient Specific Implant is that if the implant is not placed in the exact intended position, it can be worse than an off-the-shelf device.
Surgeons of find that Patient Specific Implants “find there place” due to the fit with the anatomy. This naturally reduces the tendency to be highly misplaced.
Kanawati et al’s (2022) peer reviewed study found “even without 100% contact area, results still demonstrated that an implant utilizing patient-specific geometry yielded significantly more stain area resulting in lower contact stresses using patient specific-cages compared to commercial cages”. This means that even if the Patient Specific Implant is misplaced, it is still better than an Off-The-Shelf implant.
No, your surgical process will be the same. 3DMorphic provide the implant and instrumentation, and a Medical Representative for intra-operative support. To go beyond the ‘standard’ process, 3DMorphic provides a virtual surgery plan and a physical biomodel to provide surgeons with better understanding of the interaction between the implant and patient anatomy.
Of course! Contact us to arrange a demonstration.
Contact us to discuss.
3DMorphic is a vertically integrated manufacturer with the capability, understanding and passion for providing the best result for each patient. If a surgeon approaches us with a tricky case, we collaborate to find the best custom solution for the patient.